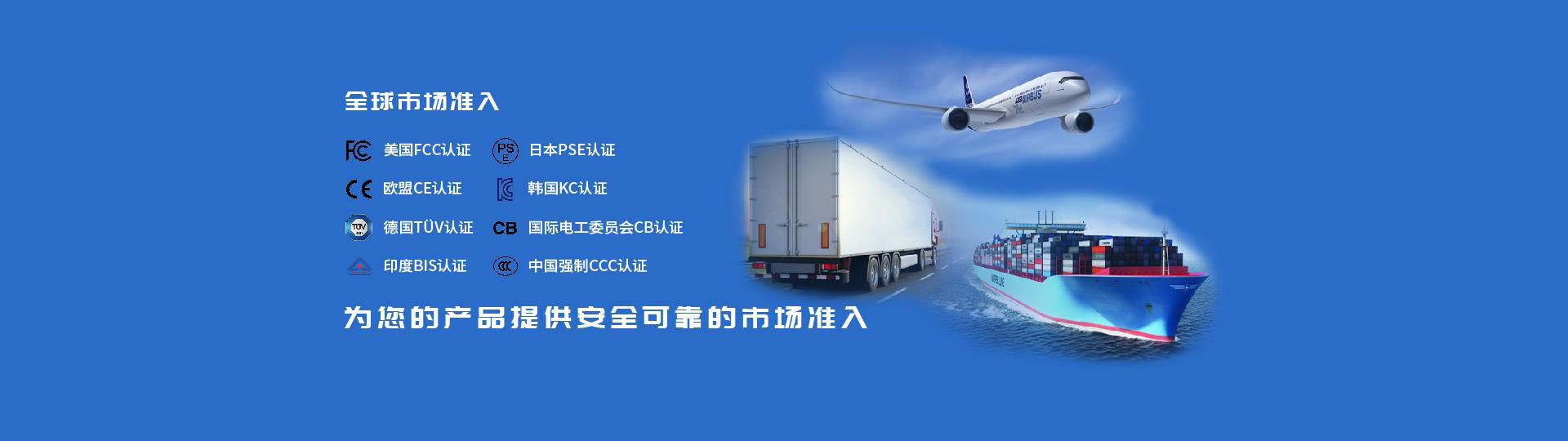
在现代工业生产中,产品的安全性与可靠性至关重要。为了确保产品在使用过程中的稳定性,企业必须进行全面的断裂失效分析。通过对材料及结构失效原因的深入研究,企业能够有效地识别潜在问题,从而提前采取措施,减少损失,保障用户安全。
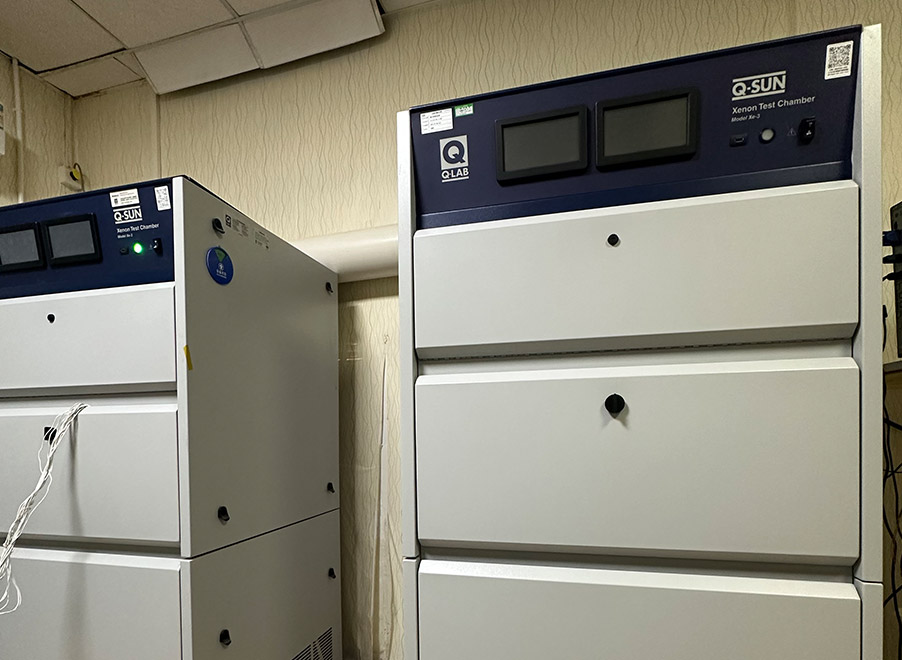
断裂失效分析是指通过对断裂样件进行检测与研究,寻找导致断裂的根本原因。这一过程不仅包括对材料的力学性能、微观结构及表面缺陷等进行分析,还涵盖了对环境因素、使用条件及设计缺陷的综合评价。通过科学的方法,研究人员能够揭示失效机理,为后续改进提供数据支持。
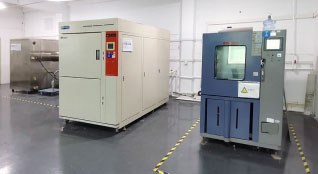
进行断裂失效分析的第一步通常是对断裂样件进行视觉检查,这一步骤有助于检测表面缺陷及初步判断断裂形式。接下来,通过显微镜观察等手段对样件进行更深入的分析,便可以找到更为细致的失效特征,如疲劳断裂、应力腐蚀等。这些细节不仅可以帮助工程师了解断裂的发生过程,还能为材料改进提供重要线索。
断裂失效分析的另一关键方面在于材料选取与设计评估。许多产品的失效往往源于材料本身的限度,例如在高温、高压或腐蚀性环境下,有些材料的性能可能会显著下降。因此,在材料选择阶段,企业需要对不同材料的特性有充分的了解,并根据实际应用需求进行合理的选择。此外,在工程设计阶段,科学合理的设计能够有效降低应力集中及采用冗余设计,进而提高产品的安全性。
倘若企业忽视了断裂失效分析的重要性,可能会面临严重的后果。发生产品失效不仅会导致经济损失,还会影响到公司声誉,严重时可能造成法律问题。因此,企业在研发和生产过程中,务必要将断裂失效分析纳入质量控制体系,确保在产品推出市场之前,对其可靠性进行充分评估。
近些年来,断裂失效分析技术也在不断发展。随着材料科学及工程技术的进步,各类先进的检测手段和分析软件应运而生,这些工具使得对断裂原因的分析更加准确、有效。同时,借助计算机模拟技术,工程师可以在设计阶段对材料的使用寿命进行预测,提前识别潜在问题,进行有针对性的改进。
综上所述,断裂失效分析是保障产品质量与安全的重要环节。通过对断裂原因的深入理解,企业可以更好地配置资源、优化生产流程,从而提升产品的竞争力。如果您还未开展相关分析工作,不妨考虑将其纳入到企业的质量管理体系中,确保在激烈的市场竞争中立于不败之地。